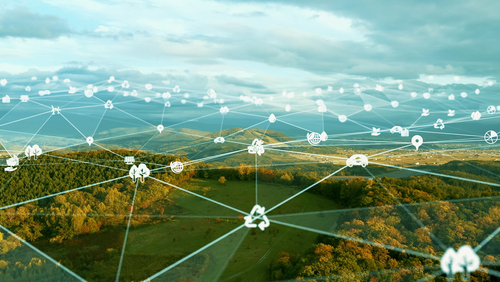
On Wednesday, a coalition of sustainable business organizations invited companies in Pennsylvania and other upper Appalachian states to participate in a produce life cycle assessment.
The Appalachian Sustainable Products Network (ASPN), a coalition of the Green Building Alliance (GBA), West Virginia University, including WVU Extension and Vantage Ventures; Catalyst Connection; Youngstown Business Incubator and BRITE Energy Innovators, said regional manufacturers were welcome to participate in a no-cost Life Cycle Assessment of their products, estimated to be worth $50,000.
Funded by the Appalachian Regional Commission’s Appalachian Initiative for Stronger Economies (ARC ARISE), and with matching funds support from the Claude Worthington Benedum Foundation, ASPN hopes to help businesses in the Upper Appalachian region meet increasing demand for products and materials used to make energy-efficient buildings and infrastructure, as well as connect buildings to a cleaner grid.
“By strengthening the reliability and growing the scope of the region’s manufacturing supply chain in sustainable building products, the Appalachian Sustainable Products Network will contribute to the regeneration of Upper Appalachia as it transitions from the extractive industries that once fueled its economy,” Jenna Cramer, president and CEO of Green Building Alliance, said.
The pilot program is looking for manufacturers of building products and/or materials to participate. The Life Cycle Assessments will measure environmental impact by looking at the entire life cycle of a product from raw material extraction to disposal. At the conclusion of the pilot program, manufacturers will receive a report with the results of the assessment, as well as a model of their product for use in identifying product design changes to lessen environmental impact.
“By engaging in a Life Cycle Assessment, manufacturers can identify opportunities to optimize resource efficiency, reduce waste, and make informed decisions regarding product design and supply chain management,” Greg Norris, GBA Vice President of Life Cycle Sustainability, said. “These studies will be for internal use by the manufacturers and should provide major and actionable insights. Each could also be later extended to support communications or certifications that open up new market opportunities, particularly in the buildings and construction industry where demand for energy efficient, reliable and green design is growing rapidly. Most significantly, this is a quantitative assessment that is the gold standard in understanding the environmental consequences of a product.”